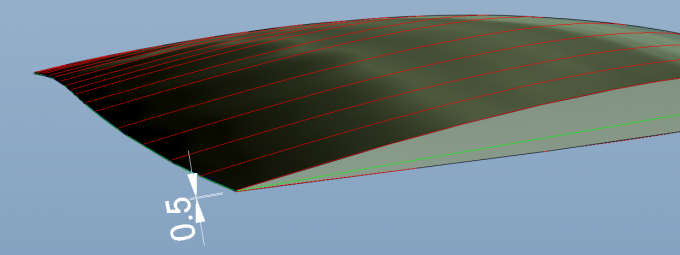
—- NEO —- ein F3F Projekt : Teil2 CAD
…nachdem die Auslegung (Link zu Teil 1 ) bestimmt war, konnte es mit der praktischen Umsetzung beginnen.
Da ich beruflich mit MegaCad 3D arbeite, bot sich an dieses CAD für die Konstruktion des Neo zu nutzen. MegaCad ist nicht so stark verbreitet und eher unbekannt, trotzdem ist es eine Profisoftware, die alles bietet und stabil läuft.
Es ist ein „direct modeler“, das heisst man baut seine Konstruktion mit Regelkörpern auf. Es muss dann nicht über irgendwelche Abhängigkeit nachgedacht werden, wie es bei parametrischen Systemen der Fall sein kann.
Mir persönlich ist das sehr sympatisch. Die Sofware kommt aus Deutschland und ist bereits seit über 30 Jahren am Markt. Auch anspruchsvolle Konstruktionen können realisiert werden.
Mit den teureren Versionen von MegaCad (ca. 5000 CHF) lassen sich Freiformflächen erzeugen. Diese sind sehr masshaltig und werden korrekt dargestellt. Es können aus den Flächen direkt Volumenkörper erstellt werden, die dann weiterbearbeitet werden können.
Günstiger wäre MegaNc. Diese Sofware beinhaltet ein MegaCad light, welches in der aktuellen 2019er Version auch Freiformflächen über Stützkurven erzeugen kann. Zudem bietet MegaNc ein CAM Modul. Preislich liegt das zwischen 1000 und 2000 CHF.
Exemplarisch möchte ich einige Details zeigen, die wichtig sind, um brauchbare Volumenkörper für die Modellkonstruktion zu erzeugen.
Es ist sinnvoll die Endleiste des Tragflügels und auch des Leitwerks mit einer definierten Dicke zu zeichnen. Beim Neo Flügel habe ich mich für 0.5mm Endleistenstärke entschieden.
Dazu zeichne ich das aus Linienstücken bestehende Tragflügelprofil als Spline nach. Als nächstes wird die Ober- und Unterseite um den Naseneintrittspunkt gedreht und zwar soweit bis am Profilende ein Abstand von 0.25 mm oben und 0.25mm unten entsteht.
Das Profil ist, durch die Drehung, minimal kürzer geworden, das wird zum Schluss mit einem kurzen gerden Linienstück ausgeglichen, sodass die Profiltiefe wieder stimmt.
Damit die Oberfläche nicht „schwingt“ müssen ausreichend Stützprofile erzeugt werden. In meinem Fall sind das 17 Stück. Je stärker die Leitkurve abbiegt, um so mehr Stützprofile braucht es. In der Regel ist das der Aussenbreich des Flügels der hiervon betroffen ist. Die Stützprofile sind rot eingezeichnet. Man erahnt, das das nicht mal schnell gemacht ist, so müssen doch die Profile 100% geschlossen sein und korrekt auf der Leitkurve (Flügelgrundriss) aufliegen.
Eine Besonderheit stellt das Flügelende dar. Hier hat es sich bewährt den Flügel nicht auf einen Punkt auslaufen zu lassen, sondern auf ein Tropfenprofil mit einer definierten Endleistenstärke (siehe nachfolgendes Bild).
Der Flügelanschluss an der Wurzelrippe wird nicht im Plexiglas gefräst, sondern durch ein Aluminum Inlet erzeugt.
Das hat den Vorteil, dass Anpassungen an der Anschlussgeometrie jederzeit vorgenommen werden können. Zudem wäre Plexiglas zu weich, wird doch dort mit dem Stechbeitel Gewebe abgestochen.
Ausgangswerkstoff für die Tragflügelform ist ein Plexiglasblock. Die Dimensionen sind hier zu erkennen:
Soweit zur CAD Konstruktion. Bei Flügel und Leitwerk ist der Aufwand vergleichsweise gering. Beim Rumpf sieht das anders aus, ist doch dieser eine richtige Fleissaufgabe.
…to be continued… mit Teil 3
Markus
Mike Gantert -
Hallo Markus
Schöner Bericht, vorallem interessant und vertändlich geschrieben. Bin auf die weiteren Berichte gespannt.
Weiter so!
Grüsse Mike
Martin Ulrich -
Danke vielmal für den Teil 2.
Spannend und aufschlussreich, auch der Einblick das mittels CAD nicht nur mal so schnell eine Tragfläche entsteht sondern es doch recht viel Können und Zeit erfordert.